

Some of the best advice I got in the Army came from a First Sergeant who said, “Never skimp on anything that protects your head or your eyes.” While the Army-issued ACH helmet offered adequate protection, the First Sergeant elected to wear a high-speed Ops-Core FAST SF helmet with an MSRP of over $2,000. The other high-speed helmet popular with troops is the Team Wendy Exfil; the latest 3.0 model retails between $1400-1900.
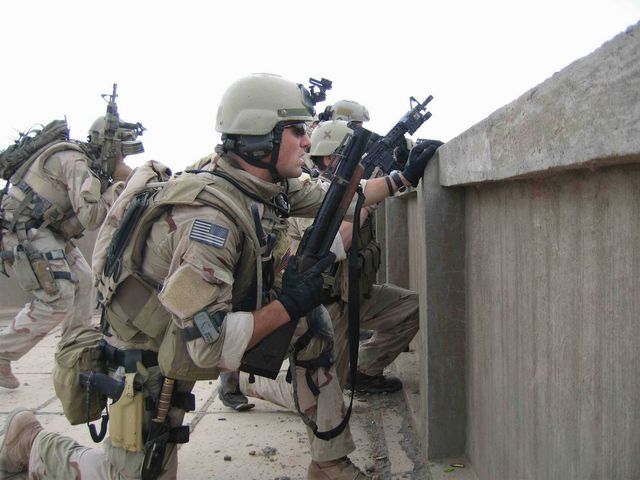
High-cut ballistic helmets like the FAST and Exfil are lighter and allow better integration of communication headsets than the MICH-style ACH and ECH. They are also made in America to ensure high levels of quality control on such an important piece of equipment. However, the cost and high demand for these high-speed helmets put them out of reach for most troops looking to purchase a replacement for their issued gear. Recognizing this gap in the market, Hard Head Veterans was started by veterans from the Special Operations community to fill it.
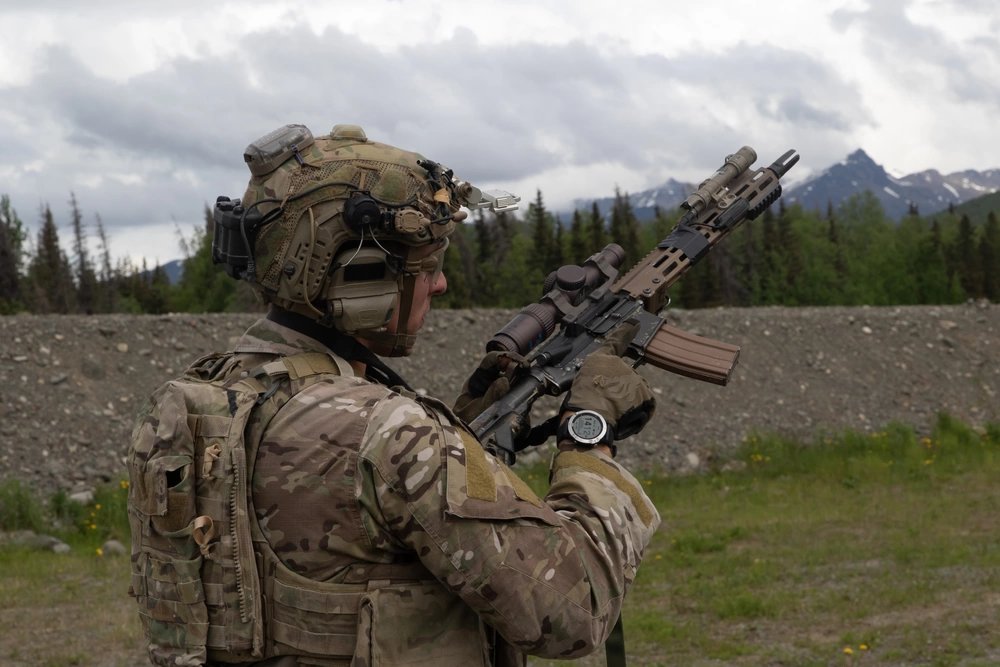
The company was founded in 2014 and began shipping product almost immediately. To accomplish their original goal of making high-cut helmets affordable and accessible, HHV’s Above The Ear helmet was pressed in China with American DuPont Kevlar or Dutch Teijin Aramid. In addition to weight savings, the ATE offered significant cost savings over the established Ops-Core and Team Wendy helmets.
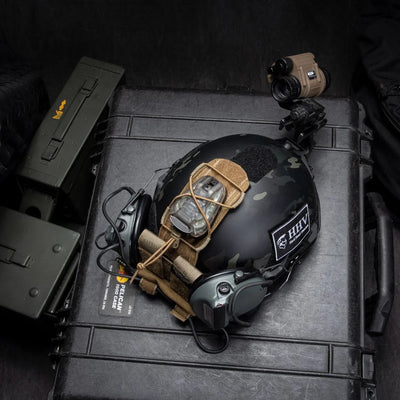
Once HHV got its start in the helmet market, the company started working on its next goal: bringing manufacturing to America. In 2020, recently retired Marine Corps veteran Carlton “Dub” Robertson moved back to Texas and was hired as HHV’s warehouse manager. “The third day that I was there, I got promoted to plant director,” Robertson told WATM. With his background in avionics, Robertson was told that he would “figure it out” as HHV stood up its manufacturing operations in Sweetwater, Texas. And figure it out, he did. Aside from some leftover equipment from the previous company, Robertson and HHV had to design and build the helmet manufacturing line from the ground up.

Today, only the ATE Gen 2, ATE Bump, and Below The Ear helmets are manufactured overseas; the ATE Gen 3, ATE Lite, and ATE Rifle helmets are manufactured in Sweetwater along with HHV’s latest product, the Kevy Hard Hat. With guidance and best practices from industry veterans, HHV takes a trial-and-error approach to product development. “It was a lot of figuring out as we went along,” Robertson recalled. The team designs a helmet, presses it, and if they like the end result, they take it out back and shoot it. Once HHV is happy with a helmet, it is submitted to NTS Technical Systems for ballistic testing.
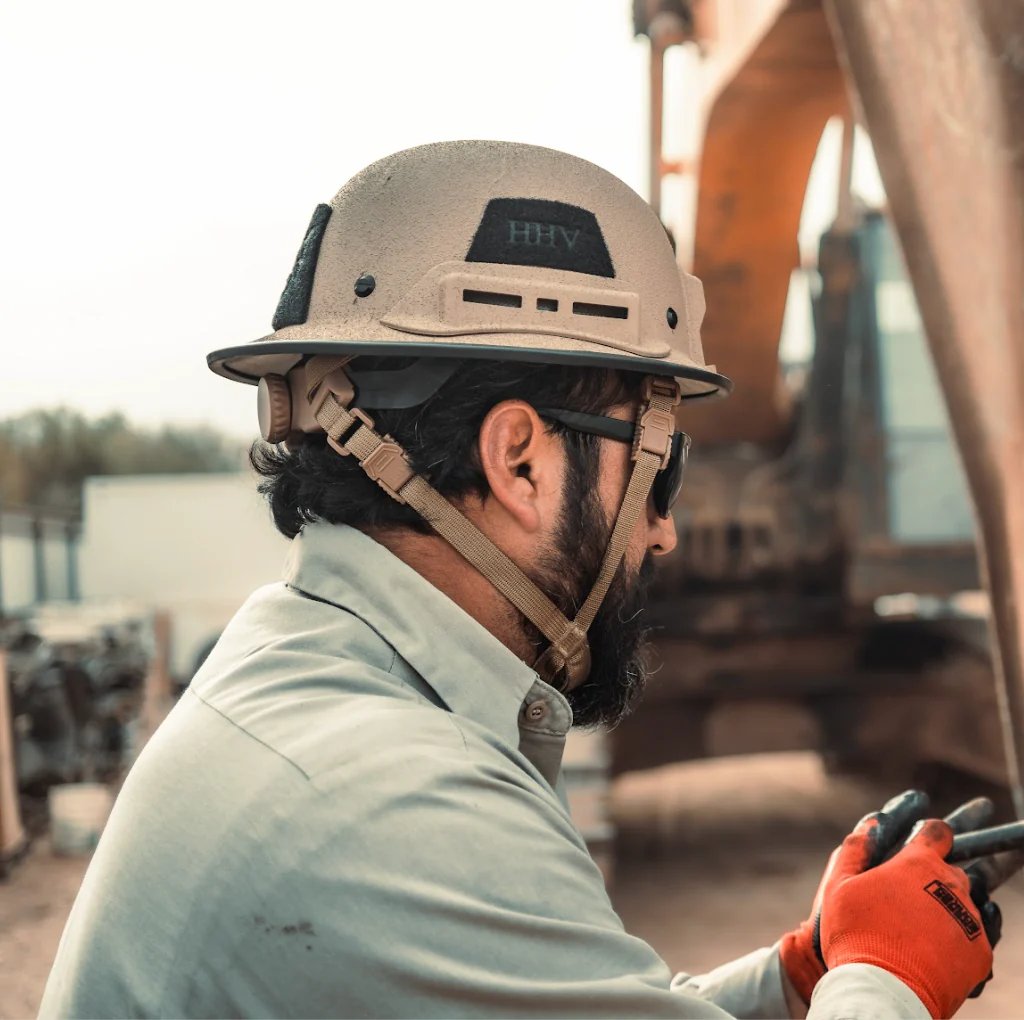
“We’re all about the customer,” Robertson asserted. “Our products focus on comfort and performance for the end user and we take pride in what we do.” Much of HHV’s production line is hands-on to ensure a personal and human connection with the life-preserving products that they put out. Going forward, HHV is working to increase the efficiency of its U.S. operations to bring domestic production costs closer to the company’s foreign production costs. As the company expands domestic production with the Kevy Hard Hat and the upcoming electrically-rated Kevy E (and maybe even a motorcycle helmet), HHV also aims to grow its domestic workforce. As of February 2025, an impressive 40% of HHV’s workforce are veterans.